The stock of chassis needed to be replenished, and I was hoping to incorporate a few minor changes and improvements to the Jonescounter this year. The main goal was to improve the reliability by making the large gear out of more robust material. Over the 7 years we’ve been selling the Jonescounter, approximately 3 % of the units sold have failed either within the first few miles, or during the first measurement. It’s impossible for me to determine whether the failures were a result of improper installation, or due to the manufacturing / design of the chassis itself. During the assembly process I give each unit several “test spins” to ensure free rotation of the gear, but it’s impractical to give each unit a test ride.
When we tried to reorder chassis parts for the JR, the supplier told us that they had lost the tooling used to produce the last order. New tooling from this supplier would have been around $20k to $25k for the punching dies, and another $15k for the forming dies. This is approximately the cost of the tooling to create the original pieces we’ve been selling.
Over a dozen manufacturers were contacted to see if they were interested in producing the chassis with slightly new specifications. Samples of the existing pieces were sent out to four likely candidates, and numerous e-mails and phone calls were exchanged until one supplier was chosen in July. After a number of very informative conversations with their tooling engineer, they produced a couple of samples.
The new chassis have the following characteristics:
The overall dimensions of the JR Counter remain unchanged. If a JR fit a bicycle before, the new chassis will still fit. The hole has been specified to allow the installation on bicycles with a 10mm axle. The first production back in ’08 only fit 9mm axles which are common in the US, but the 10mm hole accommodates many international bicycles.
The large gear is now 1.95 mm (14 ga) stainless steel, over twice the thickness of the former large gear. This increased thickness will substantially increase the strength of the drive tang, which has had a very small but disappointing failure rate, usually due to bending. Stainless Steel was chosen over carbon steel because of the wearing characteristics of various steels in a dry-bearing.
The Chassis will be available in right-hand and left-hand configurations. This will eliminate the need for an additional “adapter plate” that substantially increased assembly time and cost. The only increase in cost for right-hand units will be due to the increased cost of the counters, which are purchased in smaller numbers.
The chassis will come to us already assembled. The three pieces will be swaged together by the manufacturer. This is the method used in the production of most of the Jonescounters sold prior to the development of the JR.
The pieces will be laser cut, instead of using the former stamping operation. This increases the cost per unit slightly, but saves the initial tooling cost to create stamping dies.
No price increase for complete counters is anticipated, but the price of replacement chassis assemblies will increase by $10.
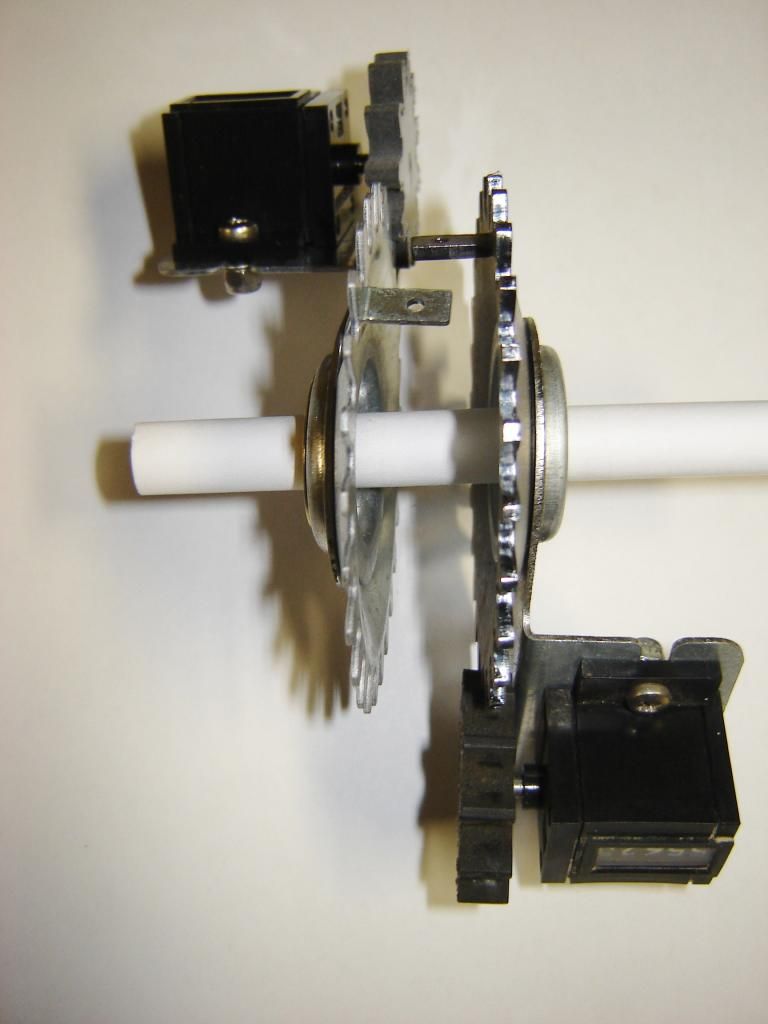
Old counter (left) and new counter (right)
Pete Riegel (shipping clerk, Jonesccounter.com)